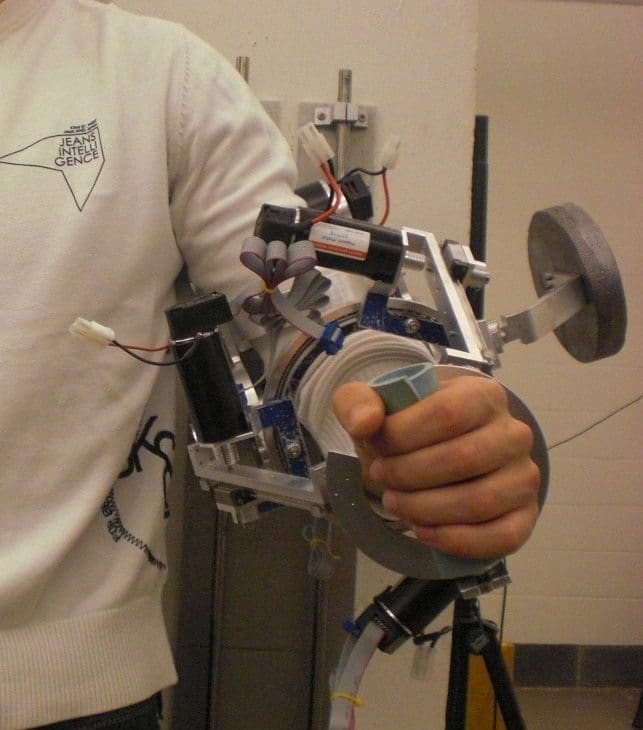
Teacher, researcher and co-founder of a startup medical robotics company, Dr. Marcia O’Malley is committed to finding engineering solutions for physical rehabilitation challenges. An Associate Professor of Mechanical Engineering at Rice University in Houston, Texas, Dr. O’Malley runs the university’s Mechatronics and Haptic Interfaces Lab (MAHI). In that capacity she is involved in multiple rehabilitation, haptic and robotic research projects, focusing on such areas as surgical skill acquisition, haptic response fidelity, and robotic rehabilitation device development, specifically the Wrist and the RiceWrist exoskeleton for arm and forearm rehab.
Challenge
Getting pilot data quickly to ensure research is well-funded
The popular notion that it “takes a village to raise a child” has an interesting corollary in the world of engineering research. Quite often it takes a diverse community of academic disciplines and institutions to bring research projects to fruition. That’s certainly true in the recent work developing the RiceWrist, a rehabilitation robot that would provide therapy and evaluate spinal cord injury patients.
“It took a lot of resources to move our project forward, says Dr. O’Malley. “But to get those resources we needed pilot data that showed we could make a good case that our robotic rehabilitation project for spinal cord injury was a worthwhile thing to pursue.”
Dr. O’Malley needed to rely on her project’s seed funding to get all the way to patient trials. That presented her with a host of challenges. She had to proceed quickly. She also was working with a very limited budget and a single research associate. As a result, she and her associate had to continuously develop their control software and refine the functionality of the rehab robot arm in order to demonstrate that this project was valuable and deserved continued funding.
Solution
Quanser's rapid prototyping, simplicity and speed are the keys
The entire process depended on rapid controller development and implementation, using Quanser’s QUARC rapid prototyping software and the Q8 card for accurate, detailed data acquisition.
Dr. O’Malley found the Q8 was an ideal data acquisition and control interface for this project
because their robotic arm has five degrees of freedom. Having one interface card plugged into one computer slot really simplified the communication from the PC to the hardware. Using one data acquisition card for all the channels allowed her to avoid the unnecessary complexity of adding several cards to get the same 5DOF information. Then, because of QUARC’s pre-defined function block sets. Dr. O’Malley was able to go from interfacing with a model to interfacing with hardware quickly.
As she put it, “The computation speed and the communication speed between the Q8 board and the QUARC environment is excellent, and completely fulfilled our needs. So we were able to gather information quickly, learn what worked and didn’t work, then implement the necessary rapid design changes to the controller.”
This was important, in part because Dr. O’Malley and her research associate were developing all this in conjunction with rehab clinicians who would be dealing with the rehab patients. The strategy they chose was to have hardware in their lab that mirrored the hardware deployed in the hospital.
”In the hospital, the therapists can actually see how well the robot works with their patients. That allowed the therapists to better articulate their needs. For example, they could tell us if they required more range of motion, more or less resistance, or some additional functionality. By using QUARC rapid prototyping software, we had a lab platform that allowed us to quickly modify and update our controller design and deliver on their changes.”
How quickly? Dr. O’Malley’s research associate could come back to the lab and implement the latest changes in one afternoon. He could then return to the hospital, upload the new controller design, test it out and it’d be ready to go for the patient the next day. “That’s how quickly QUARC enabled us to refine and implement our controller design. The speed of QUARC is an important key to the whole development process.”
By working with the therapists and patients early in the process, Dr. O’Malley and her associate were able to enact continuous improvement on the hardware and software interface. They’re currently collecting data from a trial with multiple subjects in a more controlled experiment and seeing really positive results of the robotic rehabilitation. “I want to note Quanser’s high level of customer support throughout our development process,” Dr. O’Malley says. It’s not uncommon for my students to get on the phone with someone at Quanser who wrote the block they’re working with. The Quanser Academic Solutions Advisor has been extremely helpful since he knows the problems we were facing, and the applications. He always connects us to the right people to solve or discuss any issue that arises.”
Result
More funding and new project possibilities
Today the rehab robot project continues to move forward. “Thanks to Quanser hardware and software, our process could be iterative and produce the best output possible in a short amount of time. We now have hard pilot data that positions us to get additional funding to develop the Wrist on a larger scale. We’ve gotten interest from a major funding foundation to move towards a more robust and viable form of the hardware. And the hospital we’re working with wants to deploy to multiple sites potentially.”
There is potential to develop this project beyond the rehabilitation realm. “Broadly speaking, the goal of MAHI is to design and develop robotic or mechatronic devices and their associated controllers to enhance or augment the human sensory-motor control system,” says Dr. O’Malley. “What we’ve learned from with QUARC and the Q8 data acquisition board can help us develop haptic interfaces coupled to virtual environments for training a wide range of new skills. It could be rehabilitation after a stroke or a spinal cord injury, or it could be a pilot learning to fly an airplane. There are some pretty significant similarities between relearning and learning. And we think we now have some pretty impressive hardware and software tools to contribute to that grander development.”