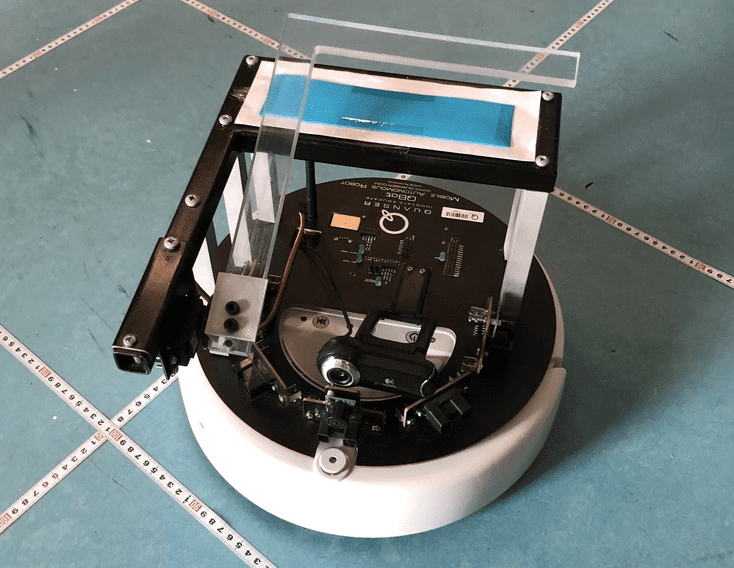
You could be forgiven for thinking that we at Quanser would never want you to “do it yourself,” since DIY implementations of servos, robots, and drones can be seen as our competitor. However, quite the opposite is true. Do it yourself, by all means, but focus on what you do best, and leave the drudge work to us.
What Does It Take To Do It?
Within Quanser, we have started to refer to the six essential products you need to get from an empty room to a modern controls teaching and research lab as the “Quanser 6-pack.” This list comprises the QUBE-Servo 2, Quanser AERO, QBot2e, QDrone, QCar, and the soon-to-be-released QArm.
Out of curiosity, I thought I would look into the total engineering time that went into getting these products to where they are today. Here are the ballpark numbers, in total engineer-years:
- QUBE-Servo 2: 2 years
- Quanser AERO: 2 years
- Qbot2e: 4 years (including the development of its predecessor, QBot2)
- QDrone: 8 years
- QCar: 6 years
- QArm: 3 years (and counting)
Can You Do the Same?
So all told, with this complete academic ecosystem, you are benefitting from over 25 years of total engineering time. And that’s not even our most engineering-heavy product line. The rotary servo product family has over 20 years of engineering time in development alone!
If you wanted to build a comparable lab from scratch, the cost in human resources and time would be staggering. This is why we can honestly say that replicating all that work – doing it yourself – just doesn’t make sense. But that doesn’t mean there’s no outlet for your ideas and creativity. I myself have been working with the QUBE-Servo 2, taking it beyond the classic control. For example, I used it as a base for experiments in visual servo control tasks using webcams. Check this out!
More Examples
We have been working on similar projects with many of our academic partners. Like here, where we developed a rotary servo-based actuator with custom sensors and a turntable:
And we have seen numerous even greater examples visiting our customers who are building on the work we have done with some great DIY teaching tools. For example here is the grand-daddy of the QBot2e, an old QBot with a custom manipulator from RMIT.
All of these are great examples of when DIY is the way to go. Application-specific development is where the boundaries of mechatronics and controls can be pushed. It is where students make real strides in their understanding of engineering practice.
Focus on What Matters to You
One of the reasons that we invested 20+ years of development in the rotary servo family is that we created a myriad of add-on modules to cover a huge range of control applications. This is simply not practical with advanced research platforms like the QDrone and QCar. In the case of those, we absolutely want you to do it yourself. Add new sensors, try different propellers, completely replace the control algorithms. This is where you get to apply your expertise! Here is an example from Aalborg University in Esbjerg, Denmark:
What we want to avoid is for your expertise to languish for years while you put together a testing platform from scratch. We spent the years of engineering development so that you don’t have to. You can get straight to experimentation and publication.
So if you’ve got a Quanser servo lying around, give it to a student design group, or maybe print out something unique to mount on the top. We want to see what you can do when you set aside the user manual and just do it yourself.